
Optimize Your Current Manufacturing Process
Benefits of Optimizing Your Current Manufacturing Process
Kurt Schneider, CFS helps brand owners of small to medium-size companies optimize their current manufacturing processes. With over 30 years of technical and operational experience in food and nutraceutical contract manufacturing, Kurt knows the nuances of production process optimization. From sourcing and product development to packaging and sales, Kurt has the expertise to help your business truly flourish.
Kurt has expertise in developing Open Innovation programs in B to C companies and has developed unique methods to accelerate product development timelines by 40% or more. When it comes to the optimization of your existing systems, Kurt is an invaluable asset.
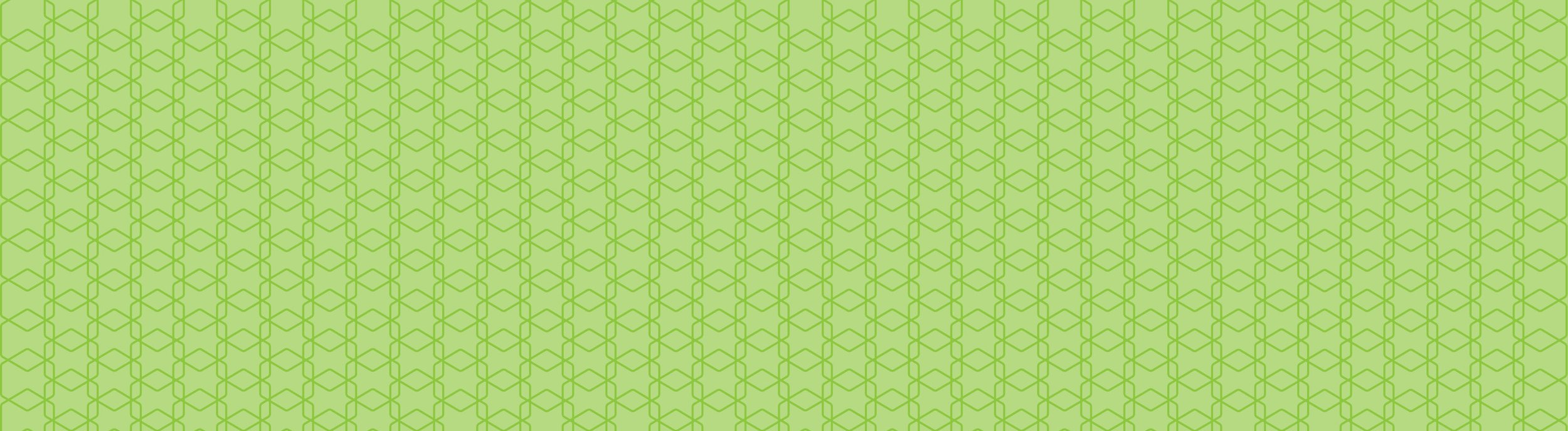
FAQs About Optimizing Your Current Manufacturing Process
-
Production process optimization is the act of refining your existing systems to decrease cost, improve production time, and increase your overall profit margin. Kurt is able to achieve this level of optimization by taking a close look at your current manufacturing processes and applying his 30+ years of contract manufacturing experience. With a background in engineering research and development, Kurt has a unique perspective when it comes to production process optimization.
-
Kurt’s best manufacturing process optimization clients have several traits in common. First off, they already have a successful product. They’ve already done the work of designing their products and bringing them to market. Secondly, they are lucrative enough to focus on optimization. They know they have a great product, but also see room for growth when it comes to their internal systems.
-
The answer for this completely depends on the scale of your business and number of products and systems you’re trying to optimize. Kurt’s manufacturing process optimization contracts take anywhere from three months to several years depending on the complexity of the project.
-
This also varies greatly depending on the goal and scope of the project. All optimization projects start with a thorough analysis of the current production process. It includes a review of all production batch records, quality testing, CAPAs (Corrective and Preventative Actions) and batch reconciliation. Once that analysis is complete, and knowing the efficiency goal required, a total project cost can be obtained.
Typically, these types of projects range anywhere from $10,000 to $30,000. Regardless of the cost of the project, the usual payback period for a production process optimization project is one year or less.
“If your issue is getting new product on the shelf before competitors, call Kurt. His company’s strategies unclog product development so product launch dates are met, instead of being dates R&D won’t try to hit and Marketing labels as fantasy. Kurt’s concise, focused and decisive in his work ethic and work style.”